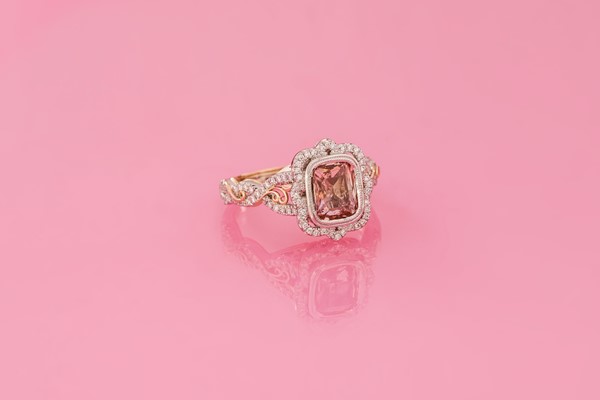
Bespoke and handcrafted, this ring is truly one-of-a-kind.
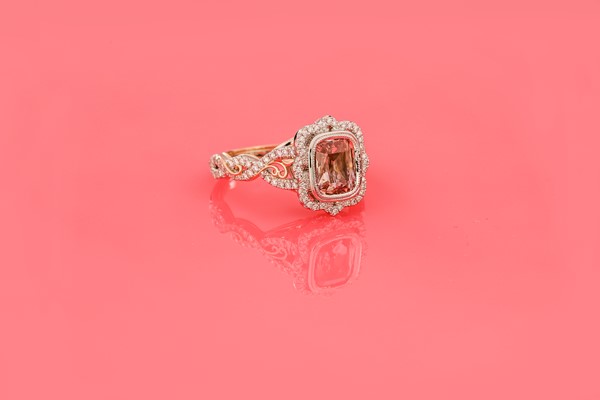
This stunning custom ring showcases a harmonious blend of two-tone metal holding diamonds and sapphires.
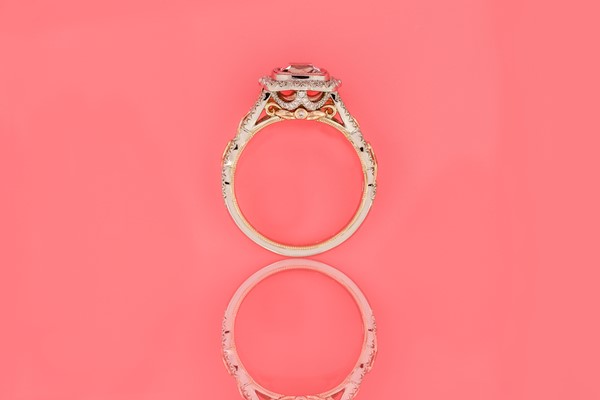
This extraordinary ring is a testament to the artistry, dedication, and passion poured into every step of the creation process.
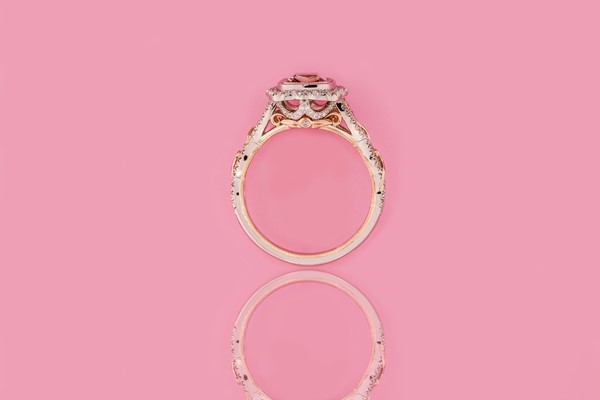
With its unique blend of exquisite design and remarkable craftsmanship, this ring is destined to become a cherished heirloom, symbolizing love, beauty, and everlasting elegance.